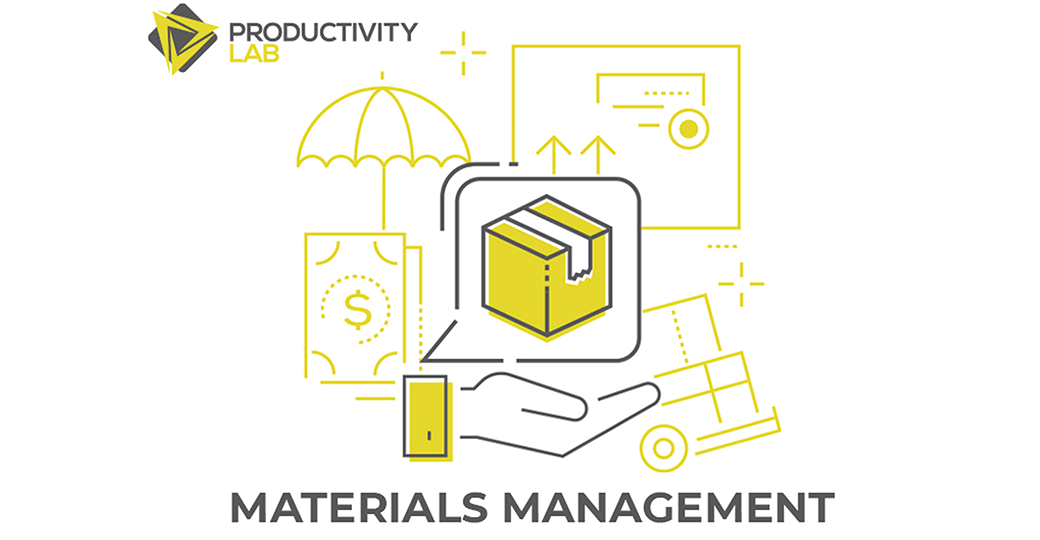
13 Oct MRO Demand Planning
MRO Demand Planning has been causing headaches across industries for quite some time, and the effects of COVID have only made the shortcomings more visible. It is time for organizations to address to start curing the headaches and realize the financial and efficiency gains tied up by not planning MRO demand adequately.
MRO stands for Maintenance Repair and Overhaul (or in many cases Maintenance, Repair and Operations is used). It encompasses all the activities used to keep your assets and facilities (and associated equipment) in safe and good operating condition.
In terms of materials, MRO can be described as the materials required to perform maintenance, repairs and overhauls on an organization’s assets or equipment, but that do not form part of that asset or equipment, and there are typically 4 categories of MRO materials:
- Production equipment maintenance and repair
- Material handling equipment maintenance and repair
- Tools and consumables
- Infrastructure maintenance and repairs
According to Tenzing, the global MRO market is estimated to be worth US$ 1.7 trillion annually, of which 12% or US$ 200 Billion is in the industrial segment. In manufacturing, MRO can represent as much as one third of a company’s spend, of which one roughly one third can be attributed to materials costs while the remainder represent costs managing and utilizing these materials.
An AT Kearney study indicates the spend on MRO materials for upstream oil and gas to be in the range of 30% – 40%.
OPERATIONS (30% – 40% of spend) | |
---|---|
Details |
|
Primary Objective | Ensure that materials are high quality, available when needed, and adhere to safety standards |
Material Management Roles |
|
Main Cost Factor |
|
Figure 1: Materials management in upstream oil and gas (reproduced from AT Kearney)
Managing the variability of demand is a core material management role in the MRO context, and demand planning is the cornerstone of managing this variability. A holistic approach to MRO materials management, built on solid demand planning:
Ensures: | Minimizes Financial Losses from: | Realizes financial savings from: |
---|---|---|
Business continuity | Higher than optimal inventories | Economies of scale in procurement |
Improved inventory control | Overbuying | Consolidation of suppliers |
Proactive maintenance | Missing items and stockouts |
Figure 2: Benefits of a holistic approach to MRO materials management
The amount of MRO stock to hold varies from company to company, and organizations across different industries might take different approaches in setting optimal or target stock levels. Some of the best practices to determine this optimal level include:
- Comparison with the replacement asset value (RAV) for all assets. Best practices suggest that the MRO inventory should be around 1.5% of an asset’s RAV.
- Economic Order Quantity (EOQ) – used mainly for materials where consumption is relatively stable, and well-known, the EOQ can be very beneficial for determining optimal MRO stock levels.
- Simulation – for critical equipment with significant supply risk, and inventory strategies for multi-asset organizations, simulation methods can go as deep as recommending ordering patterns for groups of materials.
There are a range of challenges to demand planning for MRO materials, 5 of which are shown in Figure 3 below:
CHALLENGE | MANIFESTATION IN BUSINESS |
---|---|
Poor maintenance planning with a high proportion of corrective maintenance / work orders | Heavy use of statistical methods in demand planning |
Maintenance and supply chain functions operate in silos with their own, sometimes conflicting, targets | Functions trying to meet conflicting targets at the expense of discovering the optimal solutions together |
Poor data quality, and poor use of supplier catalogues for non-mastered materials | Inefficiencies in the procurement process, duplicate and obsolete parts lingering in the systems, and heavy use of free-text Purchase Orders |
Inefficient material management processes and systems, including technology usage | Low inventory accuracy |
Poorly executed or missing MRO business process (e.g., returns, rentals, third-party repairs, preservation, and kitting) | Constant ‘noise’, taking focus away from material management teams’ main objective (See Figure 1) |
Figure 3: Challenges to MRO demand planning
Mitigating these challenges are key to implementing successful demand planning, and realizing the inherent value tied up in the above inefficiencies.
COVID has brought the above issues to the forefront due to the significant changes in demand and buying behaviors that have been experienced, and Jim Owens, senior vice president of supply chain solutions and service at SDI most likely hit the nail on the head in saying about the situation: “It underscores the need to make one person accountable for outcomes. Now is a good time to get away from the model where every group has its own agenda.”
And this is indeed, one the major challenges with demand planning, not just for MRO materials. Figure 4 highlights a typical set of conflicts occurring when discussing demand planning and execution.
Figure 4: The demand planning conflict of interest
So, how to improve? Outsourcing is becoming a more and more preferred option, and Peerless Research Group in their 2018 MRO study asked the respondents from a range of industries regarding benefits of managing MRO internally or using a third party:
Figure 5: Benefits of handling MRO management internally or through third part (reproduced from Modern Materials Handling – MMH)
Greater control and cost appear to be the biggest reason for keeping MRO management in-house, whereas the major benefit for using a third party appears to be to focus on core business. It is worth noting however, that there is a relatively low rate of respondents that sees benefits outside of this.
With regards to demand planning specifically, the challenges raised in Figure 3 must be overcome, and there is a big chance that outsourcing MRO management will not help raise these issues.
Going it internally and considering activities that can be done with a minimum of investment and new technology (although technology can help in most cases), there are 5 recommended activities to improve demand planning of MRO activities. The activities can be addressed individually, or for a larger effect, addressed collectively on a project basis.
- Review & identify new demand drivers to determine the appropriate demand planning techniques to use and make necessary changes to the forecasting models
- Improved S&OP processes (Integrated Business Planning / Integrated Demand Planning), including all relevant stakeholders, and removal of silos between supply chain and maintenance
- Establish clear business processes and procedures for demand planning and other MRO processes (returns, kitting, rentals, preservation etc.), and associated management systems including routine walk-downs and meaningful cycle counts (a meaningful cycle count is one done to drive actions to improve accuracy, not for material management functions to show 100%).
- Clean master data for MRO materials, combined with supplier catalogues where mastering is not appropriate
- Reduce complexity of what is purchased through improved MRO material segmentation, and the subsequent consolidation of MRO suppliers
For the best results, the change management component should not be underestimated. Improving demand planning requires significant behavioral change to maximize the benefits.
Alan Aastorp has built capabilities and delivered performance improvements for over 20 years, including engagements with some of the world’s largest companies, as well having professional qualifications in Supply Chain Management, Finance and HR. Alan can be reached at aastorp@productivity-lab.com.
References
Limble. (2020). An Introduction to Maintenance Repair and Operations (MRO). [online] Available at: https://limblecmms.com/blog/mro-maintenance-repair-and-operations/? [Accessed 10 Oct. 2021].
www.scmr.com. (n.d.). What Covid-19 has changed in maintenance, repair, and operations (MRO) parts management. [online] Available at: https://www.scmr.com/article/what_covid_19_has_changed_in_maintenance_repair_and_operations_mro_parts_ma [Accessed 10 Oct. 2021].
Tenzing. (n.d.). Introduction: What is MRO and why is it important? [online] Available at: https://tenzingconsulting.com/7-key-mro-insights-every-cpo-should-know/.
Sandall, R. (n.d.). Five Common Challenges in the MRO Value Chain. [online] www.innovapptive.com. Available at: https://www.innovapptive.com/blog/five-common-challenges-maintenance-repairs-operations-value-chain [Accessed 10 Oct. 2021].
www.rs-connectedthinking.com. (n.d.). MRO fuels efficiency in oil and gas. [online] Available at: https://www.rs-connectedthinking.com/en/procurement-strategy/sector-best-practice/utility-power-and-communication/mro-fuels-efficiency-in-oil-and-gas? [Accessed 10 Oct. 2021].
www.mmh.com. (n.d.). Annual Maintenance Repair and Operations (MRO) Survey 2018: Spending on the rise. [online] Available at: https://www.mmh.com/article/annual_maintenance_repair_and_operations_mro_survey_2018_spending_on_the_ri [Accessed 10 Oct. 2021].
Hoberg, K.A. and K. (n.d.). 7 Actions to Drive Demand Planning During the COVID-19 Pandemic and Prepare for the “Next Normal” – Supply Chain 24/7. [online] www.supplychain247.com. Available at: https://www.supplychain247.com/article/7_actions_to_drive_demand_planning_during_covid19.
www.kearney.com. (n.d.). Read @Kearney: Materials management: gold mine for upstream oil and gas. [online] Available at: https://www.kearney.com/energy/article/?/a/materials-management-gold-mine-for-upstream-oil-and-gas [Accessed 10 Oct. 2021].
onupkeep. (n.d.). Maintenance, Repair, and Overhaul (MRO) Explained. [online] Available at: https://www.onupkeep.com/learning/maintenance-terms/maintenance-repair-overhaul? [Accessed 10 Oct. 2021].
Gra.net.au. (2021). As Good as Gold – How to optimize your MRO supply chain with 4 unique considerations | Insights & Publications | Resources | GRA. [online] Available at: https://www.gra.net.au/resources/insights-and-publications/2020/02/161-as-good-as-gold-how-to-optimise-your-mro-supply-chain-with-4-unique-considerations? [Accessed 10 Oct. 2021].
www.mckinsey.com. (n.d.). Resetting supply chains for the next normal | McKinsey. [online] Available at: https://www.mckinsey.com/business-functions/operations/our-insights/resetting-supply-chains-for-the-next-normal.